Warren Buffett Takes A New Model Construction Approach.
The modular design emphasises Danny Forster & Architecture. New York has worked on the Module Activation Platform (MAP), a system designed to eliminate some of the barriers to large modular buildings, together with MiTek a construction company controlled by Warren Buffett’s Berkshire Hathaway. While modular construction can save time and money, there are no shortcomings. It can be prohibitively costly for shipping ready-made rooms, and leaks have taken place in some buildings. Moreover, the still rare process is impeded by zoning constraints and bureaucratic bureaucracy.
The solution for MiTek is to build flat kits with all the necessary components that contractors can easily deliver and assemble when they arrive. Due to the post-COVID immovable boom in many areas, the technology could be extremely useful. Todd Ullom, MiTek’s modular vice president, stated, ‘Communities throughout the country are in dire need of homes and that needs can be fulfilled by modular means.’ According to Ullom, MiTek can cut the bureaucracy by “collaborating with municipal officials and contractors certified by MWBE.”
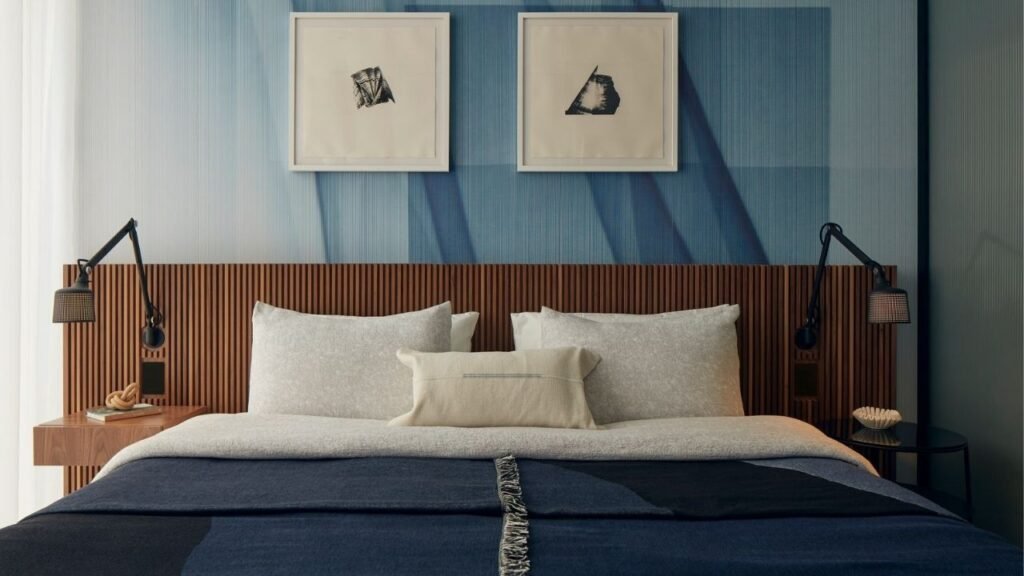
In its Chesterfield, Missouri plant, the company aims to automate the construction and transform the building into something similar to the automotive assembly line of Henry Ford. According to MiTek, MAP will make “fearless use of modular construction” for developers and architects, bringing “half a century after first being declared as the next big thing,” the mainstream. In conjunction with MiTek’s R&D and new market expansion groups, DF&A will be overseeing design and research.
“We’ve been here a couple of years,” Forster, recently approved in San Francisco for the construction of a slender modular tower, told AD.
“Under the last decade, not every building that we saw always stood on its own two feet. We acknowledged the need for a better and better process.” The problem here is that while modular designs are designed to solve problems, their limited use implies a need for unique innovation for each project. “So, you’re not transferring project-to-project information,” Forster explains.
“If this is going to be the future, not just one or two companies could do it.” I want to see more businesses using modular construction. In contrast, he rejects the concerns that the modular construction of the industry will produce cookie-cutters.
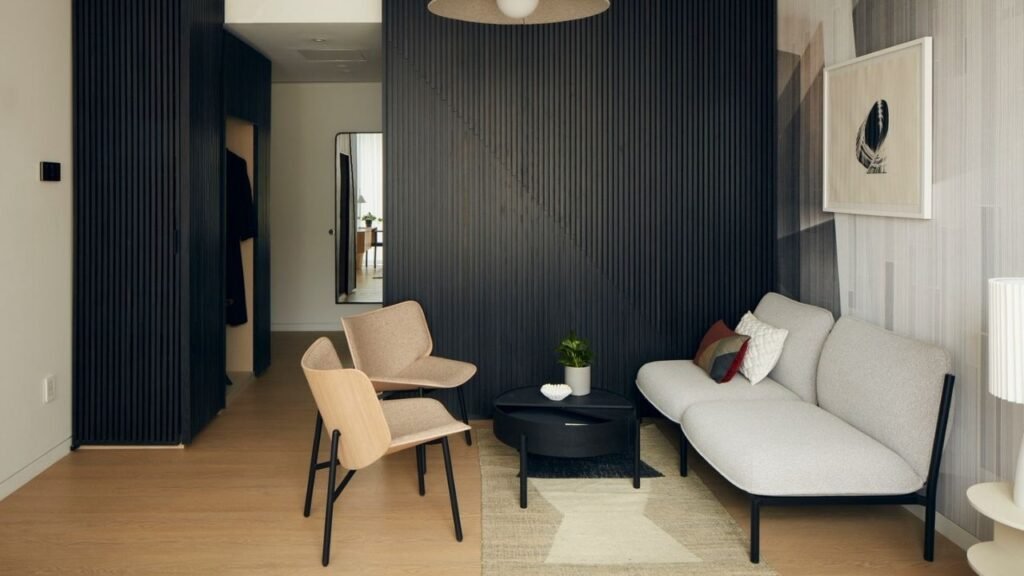
“The aim is not to set up a one size box that will fit all over America but to create a system for architecture,” Forster said. “I’m an architect trained in Harvard,” explains the author. We are going to build modular modules that do not look like a cookie-cutter. It’s aesthetic, it’s a system.”
Written By Mahak Jain | Subscribe To Our Telegram Channel To Get Latest Updates And Don’t Forget To Follow Our Social Media Handles Facebook | Instagram | LinkedIn | Twitter. To Get the Latest Updates From Arco Unico